INTRODUTION
The use of grain seeders has very ancient origins, since they have been used in Chinese agriculture since remote times (Ortiz-Cañavate, 1989). One of the first sowing machines was that by the Spanish José Locatelli, who in 1636 performed a test in Vienna. This seeder consisted of a spindle with distributor of spoons. Later, in 1701, they began to be introduced and developed in England by the English agronomist and inventor JethroTull(Sayre, 2010).
JethroTull decided to try a system based on a hoe dragged by horses, since he considered that animal traction could speed up the planting process. This process allowed him to unite two phases, the one to remove the soil and the one to deposit the seed. Thus, his planter was born, a tool that allowed, with little human work force, to till and sow extensive fields. In addition, it distributed the seeds regularly thanks to a mechanical barrier that distributed them in rows, and that reduced the need to cultivate the field to eliminate weeds (Sayre, 2010).
With the arrival of the Industrial Revolution in the nineteenth century up to date, several types of seeders have been developed for agriculture with different operating principles and various types of metering mechanisms, which guarantee both, delivery standards and uniform covering of seeds (Garrabou, 1994). In order to achieve efficiency in the sowing work, the machines are provided with auxiliary work organs that can cut the crop residues in the field to avoid jams in the machine, fertilize, dose and regulate the seed delivery, cover the seed and compact the planting line if necessary.
Soil preparation and seed quality (Cabrera et al., 2017; Quevedo et al., 2018) are prime factors to be taken into account, since they define the percentage of plants germination and their vigor, which have a direct impact on crop yields. Finally, planting density, depending on the type of seed to be planted and its sowing frame, establish the population of a field (Alvarez, 2016; Cañadas et al., 2016) and they are parameters that are defined by the dosing mechanism and the distance between rows. The sowing density should be focused on an optimal use of the sowing area, to have adequate yields.
In Cuba, mechanized planting technologies have been used, mainly after the triumph of the Revolution, that seeders of several foreign brands have been acquired, because their manufacture in the country has been limited by the lack of materials and technological limitations. Only some models of seeders of animal and mechanized traction have being developed as part of local solutions to the need of mechanizing sowing to increase productivity.
Taking into account this problem, MINAG oriented the task of reproducing a grain seeder from a manufactured model by an independent producer, in the municipality of Cifuentes, Villa Clara Province, since it was in operation with good results, little complexity, but efficient planting. Also, because the existing planters in the province (Gaspardo of Italian manufacture) presented breakage problems and the acquisition of their components was impossible or difficult. Taking these aspects into account, the objective of this work was to redesign the conventional grain planter "GUAJIRO AM 2010-1-5T".
METHODS
The redesign of the seeder consisted in the modification of the systems of transmission and dosing, as well as of the cappers and markers, for which the following methodologies were used.
Methodology for Calculating Transmission and Working Bodies
Calculation of Chain Transmission. The calculation of chain transmissions was made using the methodology established by Mott (2006), taking the following variables as reference:
Dp: diameter of the motor wheel, m; Nrm: number of holes for the corn roll, dimensionless; Nrf: number of holes for the bean roll, dimensionless; Z1: number of teeth of the conductor sprocket, dimensionless; Z2: number of teeth of the driven sprocket, dimensionless; i: transmission ratio, dimensionless.
Methodology for the Calculation of Markers
The seeder is designed to sow between two ridges, that is, from0.45 m a 0.90 m. The two possible scenarios were:
For a marking of the tire closest to the sowing line, use -b and to mark the tire farthest from the sowing line, use + b.
Methodology for the Analysis of Resistance by MEF
To carry out these analyses, both, in the structure and in the work organs of the planter, the use of the finite element method was used (González et al., 2017; Alves, 2018). The methodological procedure used was described by Abreu et al. (2015) and Medina et al (2017). It included the creation of the virtual model (3D),material assignment, meshing, virtual simulation and processing of results.
Virtual Model. A virtual (3D) model of the planter was generated through the Mechanical Desktop 2008 program, and the finite element method was used in the SolidWorks 2010 software for resistance calculations.
Border Conditions. As a second step, the border or edge conditions of the virtual model were defined. In this case, three points of attachment of the planter to the tractor bars were taken as fixed coupling, that is to say, lateral bars and third attachment point. A force of 14 kN was applied directly to the work organs, equivalent to the tractional force of the tractors belonging to the traction class of 14 kN.
Meshing. The discretization of the physical model was made from a free mesh (Figure 1), by using quadratic elements of high order with four Jacobian points, for which a total of 68 782 elements with 134 224 nodes were generated. The calibration of the mesh density was carried out according to the procedure described by González et al.(2014) andBerrios& Franco (2018).
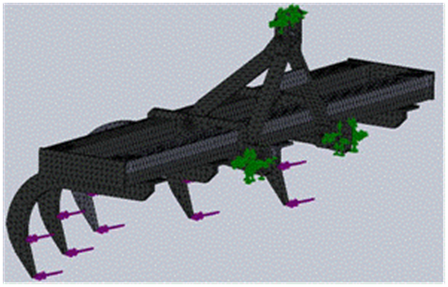
FIGURE 1.
Virtual model mesh.
Methodology of Experimental Investigations
Once the calculation and design of the work organs to be modified was completed, a prototype of the perfected planter was built, which was tested in laboratory conditions (static) and in the working conditions in the field (Portales, 2017).
The plots where the sowing took place are located within the Self-Consumption Farm belonging to “Empresa de Desmonte y Construcciones” (EDESCON). Two parcels (I and II) with brown carbonated soil were used.
The sowing of the corn was done in plot I, which has a slope of 2%. The average sowing depth was 0.08 m
In the case of beans, sowing was carried out in plot II, with a slope of 1.2%. The average sowing depth for this crop was 0.10 m.
The testing of the planter was carried out according to the regulations established in NC 34-51: 87 (1987), and NC 34-41: 04 (2004).
Determination of Test Conditions NC 34-51: 87
According to this norm,first, the test conditions are described, that is to say, all referred to soil, relief, work, among others, as well as the characteristics of the material to be manipulated by the working organs of the machines.
Carrying Out the Tests of the Grain Seeder NC 34-41: 04
The tests were essentially aimed at determining the precision in the seed plantation and the efficiency of the distribution. The following types of tests were carried out:
Static Test (Laboratory)
With the sowing unit in a stationary position, the mechanism will rotate a rotation speed equal to that of work, considering the theoretical speed of advance of the machine and the adjustment of the ratio of the dosing mechanism. A band was placed under the distributor organ of the planter, on which the seeds were dropped. The linear speed of the band was equal to the advancement speed of the planter, when moving without slippage.
As the control of the spacing of the seed is obtained by a combination of the number of holes and its speed of rotation of the dosing member, the tests were carried out for different speed ranges. The measurements of this control covered a total working distance corresponding to a minimum of 250 seeds in situ. Three organs spaced at 0.90 m were used for the working width.
In addition, other variables were determined asq (the sowing capacity, kg/ha) and Str (damaged or crushed seeds,%).
Trial Test in the Field
By means of this test, other variables that affect the redesign of the grain planter were determined, being:
V: average aggregate speed, m/s; distance between seeds, mm; G: total germination, %;(X: arithmetic average of sowing depth, mm; and distance between rows, m.
Methodology for the Economic Effectiveness of the Planter
The calculation of the economic effect (ACC., 1984), was made by means of the following equations:
E
- Economic effect, CUP;
GR1 y GR2
- Reduced Costs per unit (previous and new technique, respectively), CUP;
Q2
- Volume of production applied to innovation, dimensionless.
Considering, that:
C1 y C2
- Cost of production per unit (prior and new technique, respectively), CUP;
c
- Coefficient of effectiveness of investments, dimensionless;
I1 e I2
- Investments per unit of product for the determination of inventions, innovations or rationalizations for the prior technique and the new one, respectively, CUP;
Substituting 4 and 5 in 3, the economic effectiveness was determined, as:
RESULT AND DISCUSSION
Design of the Transmission System. It comprised the use of a transmission of power by chain of step 25.4 mm by its dimensional and constructive characteristics making it suitable for work in humidity and in contact with particles that could drain through the spaces between links. In addition, it shows a longer time of lifespan with respect to other string numbers.
The field wheel of the planter serves as a motor source (Figure 2), where two sprockets were mounted that combine with othertwo mounted to the distributor shaft, giving the possibility of four working positions (Table 1). The field wheels were made of steel with diameter of 0.37 m with spikes on the running surface to reduce slippage; the wheels were mounted on deep groove ball bearings.
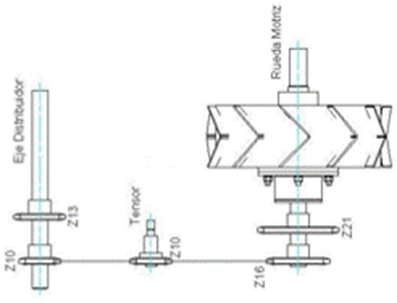
FIGURE 2.
Scheme of transmission of the seeder Guajiro AM 2010-1-5T.
TABLE 1.
Transmission ratio of the seeder
Transmission combinations | ||
---|---|---|
Sprockets wheel | Sprockets distributor | Transmission ratio, |
Z=16 | Z=10 | 1.60 |
Z=21 | Z=1 | 1.61 |
Z=16 | Z=13 | 1.23 |
Z=21 | Z=10 | 2.1 |
Design of Markers. The results obtained indicate that, to comply with the distance regulation between rows, the markers must have regulation from 0.64 to 1.09 m (Figure 3). Markers were added to the new planter, these are adjustable for sowing in frames from 0.45 m to 0.90 m. The dosing system was modified in terms of its components, to achieve greater regulation depending on the types of seeds to be used. Hinge and metal plate cappers were added since those that owned the planter were chain and did not achieve a uniform cover.
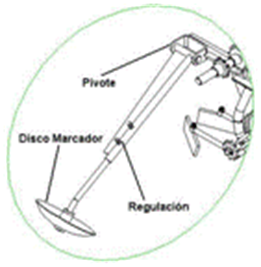
FIGURE 3.
Detail of the designed marker
Design of the Dosing Organ. This organ is composed of two interchangeable rollers of High-Density Polyethylene (Table 2), with variations in the diameters of the holes according to the dimensions of the seeds.
As an initial step to the manufacture of the rollers, a cylindrical mold was made to obtain the semi-product by injection. Later, machining was used for the conformation of the final geometry (Figure 4a) and the outer diameter and the holes were established. A splitter device was designed exclusively for this case. Finally, the threaded hole was made to fix the roller to the distributor shaft.
A rubber limiter (Figure 4c) was added to the system to remove the excess of seeds on the grooves and decrease mechanical shear damage. The modifications made offer the possibility of achieving greater versatility in the planter, improvement in treatment of the seed by decreasing the percentage of damaged seeds when using plastic as the material for the rollers. In figure 4b, an overview of the assembly of the rollers and other elements of the planter is shown.
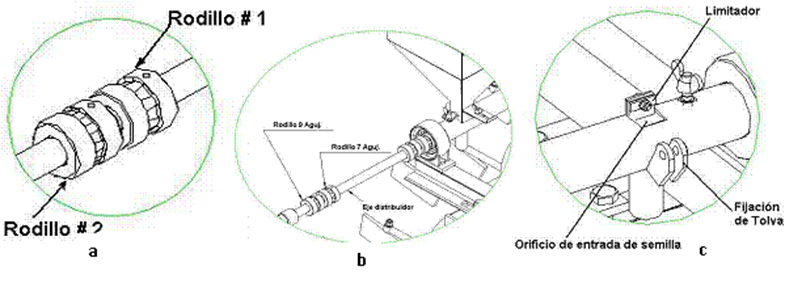
FIGURE 4.
Location detail of the distributor rollers on the distributor shaft
TABLE 2.
Feature of the rolls made
Rollers # | Slit section area, (frod); (mm2) | Number of slots, (Z); dimensionless | Work length, (lt); (m) | Coefficient of filling, (β);dimensionless |
---|---|---|---|---|
1 | 791.28 | 7 | 17 | 0.85 |
2 | 706.50 | 9 | 13 | 0.90 |
Result of the Resistance Analysis. The most loaded areas were the inner arcs of the furrowers and the points of coupling of the planter to the bars of the tractor (Figure 5), reaching stress of 41 329.61 to 74 393.29 kPa, that is to say, the areas where the direct action of external charges and their reactions were received.
However, the analysis of the distribution of the safety factor showed that the structure of the planter was able to withstand the stresses that arise during work by exhibiting a factor value of 2.2 in these areas. This value is considered satisfactory for this type of design (García& Castrillon, 2016).
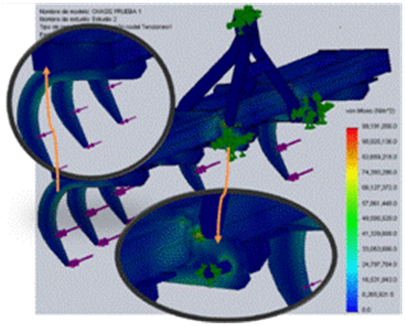
FIGURE 5.
Distribution of von Mises stresses.
With respect to the results of the deformations, the maximum values that oscillate between 1.29 to 2.42 mm were shown; these values were recorded in the area of coupling with the tractor. As it is logical, the ends of the furrower organs had the greatest displacements, from 1.05 to 1.41 mm, since they coincide with the zone of direct interaction of the working organ with the ground.
Results of Experimental Investigations. Description of the Work Process. The planter can work on tilled soils with low incidence of crop residues, as it does not have straw mince discs and it can plant on flat terraces or on beds. The furrowers openfurrows of constant depth up to 0.15 m, which can be varied according to the requirement of the crop. Later, the cappers cover the sowing line. In addition, it has regulation possibilities for the distances between rows and between plants, caliber of the seeds to plant and depth of work (Figure 6).
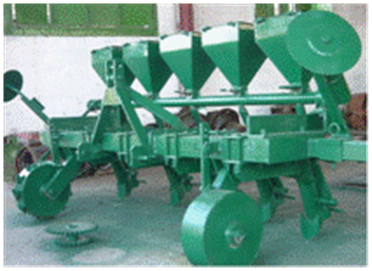
FIGURE 6.
Prototype of the planter GuajiroAM 2010-1-5T.
Results of the Tests. The sowing capacity test was carried out taking into account the possibility of regulating the working width depending on the type of crop (Table 3). That evidenced that the planter was able to comply with the dosage of seed in a range of working speeds from 1 to 3.0 m/s, guaranteeing a delivery that ranges from 24.80 to 93.02 kg/ha. Those ranges comply with the regulations and agrotechnical requirements established for planting corn and beans in Cuban agriculture.
TABLE 3.
Working capacity of the planter
The comparison of the performance of this machine with other similar ones, showed that it exhibited indicators of productivity and quality of work (García& Castrillon, 2016; Macedo et al., 2016), similar to the mechanical seeding machines that have been imported in Cuba, for grain sowing, as well as in other countries.
The statistics of the results of evaluating the irregularity of the delivery showed that it complied with the standard requirements for this aspect.
The evaluation of mechanical damage showed that it wasgreater in corn seeds, but it was within the allowable percentage for seeders of mechanical distributor (3%). The distances between seeds were taken directly from the furrow once the plants germinated. They were146 mm for corn and 69 mm for bean.
The average depth in both cases agreed with the desired results, adjusted to the requirement that the depth of sowing must be three times the diameter of the seed. It was 28.1 mm for corn and 16.8 mm for bean. Equally, the distance between rows (ridge) was measured, and it was in both crops 0.90 m, which agreed with the requirements and with the distance set in the furrowers.
Result of the Economic Effect of the Prototype Production. The results of the elaboration of a cost sheet showed that the -5T amounted to 2 997.00 CUP (National Currency), which is equivalent to 1 000 USD according to the established conversion rate (1 USD = 3 CUP) in the Program More Food Cuba (GELMA, 2004).Table 4 shows the analysis of the cost and investment elements included in equation (5).
TABLE 4.
Values of the variables for the calculation of economic effect
The determination of expenses of the previous machine evidenced that the average costs of acquisition of the sowing machines imported nowadays for the Cuban agricultural sector were around 5 500.00 USD.
Taking into account these figures and solving the equation (3), the economic effect for each manufactured machine was equal to E =4 500.00 USD, which is interpreted as the economic repercussion of the production of a technology that substitutes the import of another similar one.
CONCLUSIONS
The redesign of the organs that define the work quality of the planter, started from the agrotechnical requirements established for the development of corn and bean crops in the production conditions under study.
The determination of the productivity indicators showed that the planter is suitable for planting beans and maize in the conditions of Cuban agriculture, since it guarantees compliance with planting standards between 24.80 and 93.0 kg/ha, in a range of speeds and sowing depth of 1.95 to 2.06 m/s and 0.05 to 0.15 m, respectively.
The determination of work quality indicators showed that the machine meets the quality requirements established for the realization of this work. The redesign of the work organs allows the work of the planter on both flat and furrowed land, adjusting to plantation frames between 0.45 and 0.90 m and maximum planting depths of 0.28 and 0.16 m for corn and beans, respectively.
The analysis of the mechanical damage caused by the mechanical distributor to the seeds showed that corn seeds were within the acceptable percentage (3%), for the seeders with this type of distributor.
The total manufacturing costs of the planter amounted to 1 000.00USD, representing a saving by import substitution of 4 500.00 USD.